What Is the Difference between HDPE and UHMWPE?
- Share
- From
- https://www.polyreflex.com/
- publisher
- Polyreflex
- Issue Time
- Jan 8,2024
Summary
Explore the distinctions between HDPE and UHMWPE to make informed decisions for your industrial projects. Discover the unique properties of HDPE sheets and UHMWPE, and find the right material for your specific application needs.
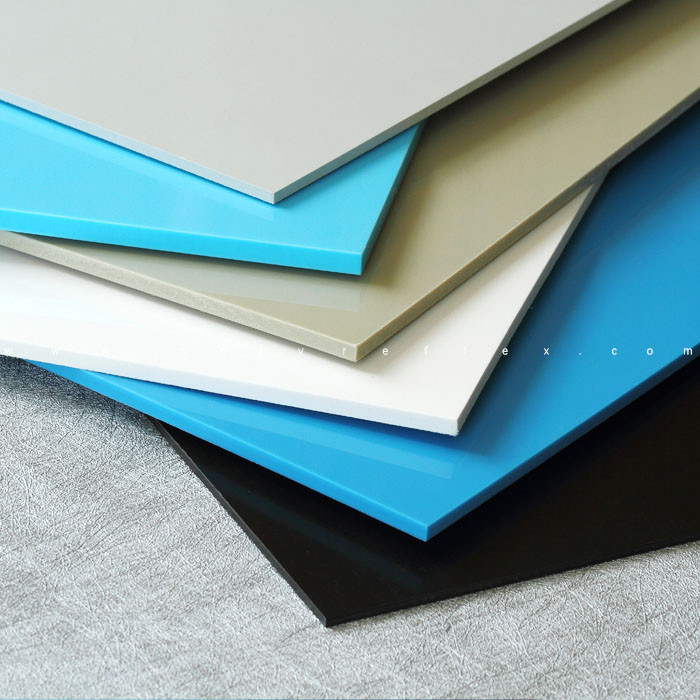
Welcome to Polyreflex, where we unravel the distinctions between two remarkable materials - HDPE (High-Density Polyethylene) and UHMWPE (Ultra-High-Molecular-Weight Polyethylene). As industry leaders in the manufacturing of polyethylene sheets, we understand the significance of choosing the right material for your specific needs. In this exploration, we delve into the unique characteristics of HDPE and UHMWPE, shedding light on their applications across diverse industries.
HDPE and UHMWPE are both integral players in the world of polymers, finding widespread use due to their exceptional properties. From enhancing structural integrity to minimizing friction, these materials have carved out their niches in various sectors. Whether you're involved in packaging, construction, industrial manufacturing, or seeking solutions for specialized applications, understanding the differences between HDPE and UHMWPE is crucial for making informed decisions.
Join us on this journey as we unravel the distinctive features and applications of HDPE and UHMWPE, empowering you to choose the right material for your projects. Let's navigate the intricacies of these polymers to ensure you make choices that align seamlessly with your unique requirements.
HDPE Sheets
UHMWP Sheets
What is HDPE?
High-Density Polyethylene, commonly known as HDPE, is a versatile and robust thermoplastic with distinctive properties that make it a preferred choice across various industries. Embraced for its high molecular density, HDPE exhibits outstanding strength, durability, and versatility.
HDPE's high molecular density grants it remarkable strength and rigidity, making it resistant to impact and external forces. This characteristic ensures the structural integrity of HDPE sheets, a quality paramount in numerous applications. Furthermore, HDPE boasts exceptional chemical resistance, contributing to its longevity in challenging environments. Its ability to withstand harsh chemicals makes it an ideal material for applications where exposure to corrosive substances is a concern.
In addition to its robustness, HDPE is renowned for its versatility. This thermoplastic material is easily moldable, allowing for various fabrication methods to meet specific project requirements. The combination of strength, chemical resistance, and malleability positions HDPE as a material of choice in diverse sectors.
HDPE's exceptional strength and resistance make it a staple in the packaging industry. Used widely in food packaging and industrial containers, HDPE sheets ensure the secure transit of products while safeguarding their quality. The material's resistance to impact and chemicals provides an effective barrier against external factors, making it indispensable in the packaging of various goods.
2. Construction
In the construction industry, HDPE sheets find applications in various forms, including geomembranes, pipes, and construction sheets. The high tensile strength of HDPE, combined with its resistance to corrosion, makes it an ideal choice for infrastructure projects. Whether used in water pipes or as a protective lining in construction projects, HDPE contributes to the creation of sustainable and long-lasting structures.
3. Industrial Manufacturing Solutions
HDPE's robust composition makes it a reliable material for fabricating components, machinery parts, and equipment casings in industrial manufacturing. The material's resistance to impact and chemicals ensures the longevity of equipment, even in challenging industrial environments. The flexibility of HDPE allows for precision molding, catering to the intricate specifications often found in manufacturing processes.
Chemical Resistant HDPE Tanks
HDPE Backing Board
HDPE Industrial Parts
What is UHMWPE?
In addition to its robustness, HDPE is renowned for its versatility. This thermoplastic material is easily moldable, allowing for various fabrication methods to meet specific project requirements. The combination of strength, chemical resistance, and malleability positions HDPE as a material of choice in diverse sectors.
UHMWPE is characterized by an exceptionally high molecular weight, contributing to its impressive strength and durability. The molecular structure of UHMWPE forms long chains, resulting in outstanding abrasion resistance, impact strength, and a low coefficient of friction. This combination of properties makes UHMWPE a material of choice in scenarios where wear and tear are critical factors.
Yellow UHMWPE
Black UHMWPE
White UHMWPE
UHMWPE's exceptional abrasion resistance makes it an ideal material for the production of bearings and gears. Its ability to withstand continuous friction without significant wear ensures longevity and reliability in mechanical systems. UHMWPE's low coefficient of friction also contributes to smooth, efficient operation.
2. Conveyor Systems
UHMWPE's low coefficient of friction and excellent wear resistance find applications in conveyor systems. Components such as rollers, guides, and chutes made from UHMWPE contribute to the smooth and efficient movement of materials along the conveyor, reducing friction and minimizing wear.
3. Specialized Components in Automotive Industry
UHMWPE is utilized in the automotive industry for specialized components where high wear resistance is crucial. It finds applications in various parts, including bushings, gears, and components in the suspension system, contributing to enhanced durability and performance.
4. Sports Equipment
The exceptional impact resistance and lightweight nature of UHMWPE make it an excellent choice for sports equipment. Components like ski bases, skateboard wheels, and protective gear benefit from UHMWPE's ability to withstand high impact forces while maintaining durability.
UHMWPE Gear
UHMWPE For Bumper
UHMWPE As Fenders For Ships
Key Differences Between HDPE and UHMWPE
In the world of polyethylene, the key differences between HDPE (High-Density Polyethylene) and UHMWPE (Ultra-High-Molecular-Weight Polyethylene) lie in their molecular composition, mechanical properties, and the specific applications where each excels.
1. Molecular Weight
HDPE: HDPE has a high molecular weight, contributing to its strength and rigidity. However, when compared to UHMWPE, its molecular weight is relatively lower.
UHMWPE: UHMWPE, as the name suggests, boasts an ultra-high molecular weight, far surpassing that of HDPE. This characteristic enhances UHMWPE's durability and abrasion resistance.
2. Mechanical Properties
HDPE: Known for its excellent tensile strength and impact resistance, HDPE performs exceptionally well in applications requiring structural integrity. It is a reliable choice for projects where moderate strength is essential.
UHMWPE: UHMWPE stands out with superior mechanical properties, including exceptional impact strength and abrasion resistance. Its molecular structure contributes to reduced friction, making it a preferred material for applications involving high wear and tear.
3. Typical Applications
HDPE: HDPE finds its niche in various industries. It is commonly used in packaging, construction, and industrial manufacturing due to its versatility. HDPE sheets are favored for their ability to withstand chemical exposure and their reliability in diverse environments.
UHMWPE: UHMWPE excels in applications where its ultra-high molecular weight is advantageous. It is the material of choice for projects involving high abrasion, such as in the production of bearings, gears, and components in conveyor systems. UHMWPE's low coefficient of friction makes it ideal for applications where smooth, low-wear movement is critical.
Simply put, the unique advantages of HDPE and UHMWPE are:
HDPE Advantages:
Versatility in fabrication processes.
Widely used in packaging and general-purpose applications.
Excellent chemical resistance.
UHMWPE Advantages:
Superior abrasion resistance.
Low coefficient of friction, reducing wear.
Ideal for high-wear applications in various industries.
How to Choose the Right Material?
When faced with the decision between HDPE (High-Density Polyethylene) and UHMWPE (Ultra-High-Molecular-Weight Polyethylene), selecting the appropriate material requires careful consideration of the specific project requirements. Each material comes with its unique set of advantages, and understanding the factors that influence material choice is crucial for optimal performance.
1. Load-Bearing Capacity
2. Wear Resistance
3. Chemical Resistance
4. Specific Application Considerations
As you navigate the diverse applications and properties of HDPE and UHMWPE, we encourage you to make decisions tailored to your unique project requirements. Whether you prioritize the versatility of HDPE or the specialized characteristics of UHMWPE, understanding the specific demands of your application is paramount.
Polyreflex stands as your trusted partner in material solutions. Our commitment to innovation, reliability, and sustainability is reflected in the quality of our HDPE and UHMWPE sheets. Explore the possibilities, weigh the advantages, and let informed decisions guide your material selection.
- Discover Endless Possibilities with Polyreflex HDPE & UHMWP Sheets
- Reach Out Now!