What Are Vacuum Forming Sheets Made of?
- Share
- From
- https://www.polyreflex.com/
- publisher
- Polyreflex
- Issue Time
- Mar 12,2024
Summary
Discover what vacuum forming sheets are made of and explore the versatility of ABS sheets for custom vacuum forming solutions. Find high-quality thermoplastic materials for your vacuum forming needs. Contact us for reliable and versatile vacuum forming plastic sheets tailored to your specific requirements.
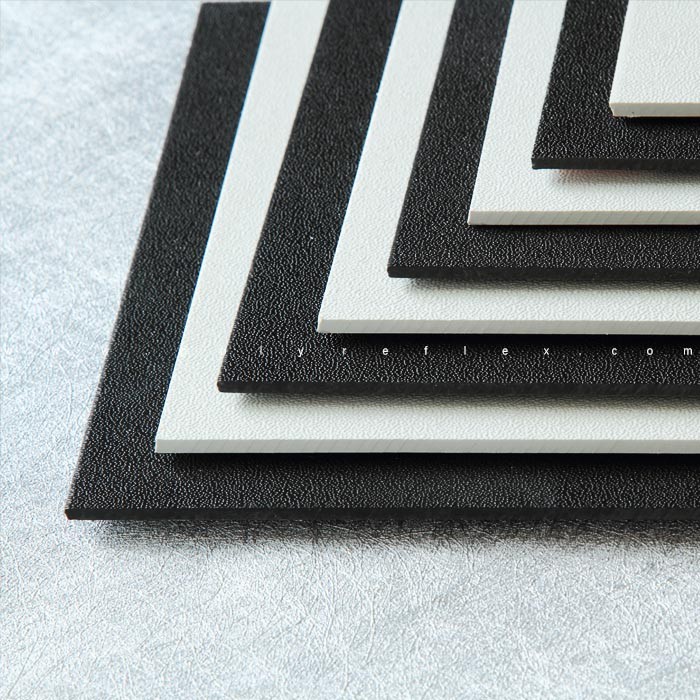
Vacuum forming, a widely used manufacturing process, involves heating a thermoplastic sheet until it becomes pliable and then shaping it over a mold using vacuum pressure. This technique is commonly employed to create a variety of products, ranging from packaging to automotive components and consumer goods.
What Are Vacuum Forming Sheets?
The process begins with a flat thermoplastic sheet, typically made of materials such as ABS (Acrylonitrile Butadiene Styrene), PETG (Polyethylene Terephthalate Glycol), or PVC (Polyvinyl Chloride). The sheet is heated to its forming temperature, allowing it to soften and become malleable. Once heated, the sheet is stretched over a mold and held in place while a vacuum is applied underneath, sucking the material tightly against the mold's surface. This results in the desired shape being formed as the material cools and solidifies.
The selection of the appropriate material is crucial in vacuum forming as it directly impacts the quality, durability, and appearance of the final product. Factors such as the desired aesthetics, mechanical properties, and environmental considerations play a significant role in material selection. Different thermoplastics offer varying degrees of impact resistance, heat resistance, and surface finish, making it essential to choose the most suitable material for the intended application.
In summary, vacuum forming sheets serve as the foundation for creating a wide range of products through the vacuum forming process. The careful selection of materials ensures optimal performance and functionality in the final product, highlighting the importance of material selection in vacuum forming applications.
Understanding ABS Sheets
ABS, short for Acrylonitrile Butadiene Styrene, is a widely used thermoplastic polymer renowned for its exceptional properties, making it a popular choice in various industries. Let's delve into the composition and properties of ABS sheets, particularly concerning their relevance to vacuum forming applications.
Definition and Composition
ABS is a copolymer composed of three main monomers: acrylonitrile, butadiene, and styrene. This unique combination of monomers results in a material with a diverse range of properties, blending the toughness and impact resistance of polybutadiene rubber with the rigidity and strength of styrene-acrylonitrile copolymer. The proportion of each monomer can be adjusted to tailor the properties of the ABS to specific application requirements.
Properties of ABS Sheets Relevant to Vacuum Forming
ABS sheets possess several key properties that make them well-suited for vacuum forming processes:
1. Impact Resistance: One of the most notable characteristics of ABS is its exceptional impact resistance. This property ensures that ABS sheets can withstand the stresses and strains encountered during the vacuum forming process, as well as in the final application. Whether forming intricate shapes or producing structural components, ABS sheets maintain their integrity and durability.
2. Thermal Stability: ABS exhibits good thermal stability, allowing it to be heated to the required forming temperature without degrading or losing its mechanical properties. This thermal stability is essential in vacuum forming, where the material must be heated uniformly to achieve optimal forming results. ABS sheets can withstand the heating and cooling cycles of the vacuum forming process, ensuring consistent performance.
3. Surface Finish: ABS sheets offer excellent surface finish characteristics, making them ideal for applications where aesthetics are important. The smooth surface of ABS sheets allows for precise molding of intricate details and textures, resulting in finished products with high visual appeal. Whether producing consumer goods or automotive components, ABS sheets deliver superior surface finish quality in vacuum forming applications.
4. Chemical Resistance: ABS is resistant to a wide range of chemicals, including acids, alkalis, and solvents. This chemical resistance ensures that ABS sheets maintain their properties and appearance when exposed to various environmental conditions, making them suitable for applications requiring resistance to chemical exposure.
Advantages of ABS Sheets in Vacuum Forming
ABS sheets offer numerous advantages when used in vacuum forming processes, making them a preferred choice for a wide range of applications. Let's explore these advantages in detail:
1. Impact Resistance and Durability
ABS sheets are renowned for their exceptional impact resistance and durability. This property ensures that ABS-formed products can withstand mechanical stresses and impacts, making them suitable for applications where robustness is paramount. Whether forming protective enclosures, automotive components, or consumer goods, ABS sheets provide reliable performance and long-lasting durability.
2. Heat Resistance and Formability
ABS sheets exhibit excellent heat resistance, allowing them to be heated to the required forming temperature without losing their structural integrity. This thermal stability enables precise molding and shaping of ABS sheets during the vacuum forming process. ABS sheets can be easily formed into complex shapes and intricate designs, making them versatile for a wide range of product applications.
3. Surface Finish and Aesthetics
One of the standout features of ABS sheets is their ability to achieve a high-quality surface finish and aesthetic appeal. The smooth surface of ABS sheets allows for intricate detailing and texture replication, resulting in visually appealing finished products. Whether producing signage, display cases, or consumer electronics, ABS-formed products exhibit superior surface finish and aesthetics, enhancing their overall appeal to consumers.
The advantages of ABS sheets in vacuum forming processes include their exceptional impact resistance and durability, heat resistance and formability, as well as surface finish and aesthetics. These properties make ABS sheets a versatile and reliable choice for a wide range of applications, ensuring high-quality, durable products that meet the demands of various industries.
Applications of Vacuum Formed ABS Sheets
Vacuum formed ABS sheets find extensive use across diverse industries, owing to their versatility, durability, and aesthetic appeal. Let's explore some prominent applications:
Automotive Industry
Vacuum formed ABS sheets play a vital role in the automotive sector, where they are utilized for manufacturing various components such as dashboards, interior trim panels, door panels, and wheel covers. ABS's excellent impact resistance, heat resistance, and surface finish make it an ideal material for automotive interiors, ensuring both functionality and aesthetics.
Electronics Industry
ABS sheets are widely employed in the electronics industry for fabricating enclosures, housings, and protective covers for electronic devices and equipment. The robustness and formability of ABS make it suitable for housing delicate electronic components while providing adequate protection against environmental factors and mechanical impacts. The smooth surface finish of ABS enhances the visual appeal of electronic devices, contributing to their marketability.
Consumer Goods
In the consumer goods sector, vacuum formed ABS sheets find applications in a variety of products, including toys, displays, and signage. ABS's ability to replicate intricate details and textures makes it an excellent choice for producing visually appealing and durable consumer goods. Whether manufacturing toy figurines, retail displays, or promotional signage, ABS sheets offer versatility and reliability, meeting the demands of diverse consumer markets.
In summary, vacuum formed ABS sheets are indispensable in a wide range of applications across industries such as automotive, electronics, and consumer goods. Their superior properties, including impact resistance, heat resistance, and surface finish, make them the material of choice for manufacturing high-quality and visually appealing products that meet the needs of modern consumers.
Production Process of ABS Vacuum Forming Sheets
The production process of ABS vacuum forming sheets involves several stages, each crucial for ensuring the quality and performance of the final product. Here's an overview of the typical manufacturing techniques:
1. Raw Material Preparation: The process begins with the preparation of raw materials, which typically include ABS resin pellets, additives, and colorants. These materials are carefully selected to meet the desired specifications for the final ABS sheets.
2. Extrusion: The prepared ABS resin pellets are fed into an extruder, where they are melted and homogenized under controlled temperature and pressure conditions. The molten ABS is then extruded through a die to form a continuous sheet of uniform thickness.
3. Cooling and Sizing: After extrusion, the hot ABS sheet is rapidly cooled using cooling rollers or a water bath to solidify the material. The cooled sheet is then passed through sizing rollers to achieve the desired thickness and width.
4. Surface Treatment: Surface treatment may be applied to the ABS sheet to enhance adhesion, improve surface finish, or impart specific properties such as UV resistance or chemical resistance. Surface treatments may include corona treatment, flame treatment, or coating application.
5. Vacuum Forming: Once the ABS sheet is prepared, it is ready for the vacuum forming process. The sheet is heated to its forming temperature and then stretched over a mold using vacuum pressure to create the desired shape. This process allows for the production of complex and intricate parts with high precision.
ABS Sheet Vacuum Forming
In conclusion, ABS sheets stand out as a versatile and reliable material for vacuum forming applications, offering a combination of strength, durability, and aesthetic appeal. Throughout this exploration, we've highlighted the various advantages of ABS sheets, including their impact resistance, heat resistance, surface finish, and suitability for a wide range of industries.
From automotive interiors to consumer electronics and beyond, ABS vacuum forming sheets play a crucial role in shaping modern manufacturing processes and delivering high-quality products to consumers worldwide. Their versatility and adaptability make them an indispensable choice for manufacturers seeking durable and visually appealing solutions.
At Polyreflex, we understand the importance of quality and reliability in vacuum forming applications. That's why we offer a comprehensive range of ABS sheet offerings tailored to meet the diverse needs of our customers. Whether you're in the automotive, electronics, or consumer goods industry, we invite you to explore our ABS sheet solutions and discover how Polyreflex can partner with you to achieve your manufacturing goals.
Choose Polyreflex for premium ABS vacuum forming sheets that deliver exceptional performance, durability, and aesthetics. Contact us today to learn more about our ABS sheet offerings and how we can support your manufacturing endeavors.
- Discover Endless Possibilities with Polyreflex ABS Sheets
- Reach Out Now!