How to Choose the Right Polypropylene Board for Your Project
- Share
- From
- https://www.polyreflex.com/
- publisher
- Polyreflex
- Issue Time
- Apr 10,2025
Summary
Learn how to choose the right Solid Polypropylene Board for your project with expert advice on thickness, mechanical properties, and industrial applications. Polyreflex offers durable, customizable polypropylene sheets perfect for a variety of industries.
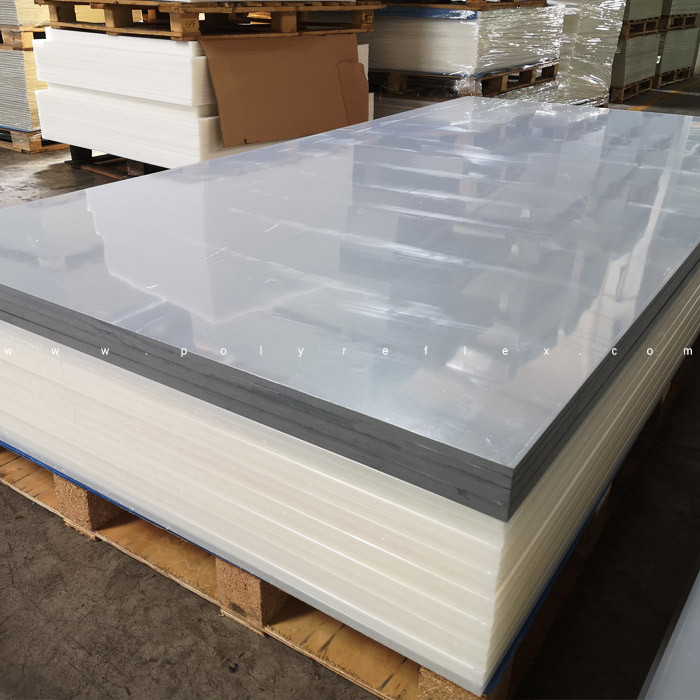
Polypropylene (PP) Board is a durable, lightweight, and highly versatile material made from polypropylene resin. Known for its exceptional chemical resistance, impact strength, and moisture resistance, PP boards are used across a wide range of industries. These solid, extruded boards offer consistent thickness and strength, making them ideal for applications in automotive, construction, chemical processing, and custom fabrication. Whether for industrial parts, protective covers, or specialized equipment, solid polypropylene boards provide reliable performance in demanding environments. In this article, we’ll guide you on how to choose the right PP board for your project, ensuring it meets your specific requirements for durability, functionality, and cost-effectiveness.
What is Solid Polypropylene Board?
Solid Polypropylene Board is a high-performance, extruded plastic material made from polypropylene resin. Unlike PP corrugated boards or PP honeycomb boards, which feature hollow structures, solid polypropylene boards are dense, uniform, and rigid, offering exceptional strength and durability. These boards are typically available in thicknesses of 3mm and above and are widely used in various industrial and commercial applications due to their unique properties.
Key characteristics of solid polypropylene boards include:
Solid polypropylene boards offer a unique combination of features that make them a reliable and versatile material for a wide range of industrial applications.
Key Considerations for Choosing the Right Polypropylene Board
When selecting the right solid polypropylene board for your project, several key factors must be considered to ensure the material meets the specific demands of your application. These considerations include thickness, mechanical properties, chemical resistance, temperature resistance, and surface finish. Below, we explore each of these factors in detail:
1. Thickness and Size
The thickness of the polypropylene board plays a crucial role in determining its strength and suitability for various applications. Boards with a thickness of 3mm and above are ideal for most industrial uses. Thicker boards provide increased rigidity and load-bearing capacity, making them suitable for heavy-duty applications like machinery parts, protective panels, and storage tanks. On the other hand, thinner boards (such as 3mm or 5mm) are often used for lighter applications like signage or interior panels. It’s essential to choose a thickness that aligns with the mechanical stresses your project will face.
2. Mechanical Properties
The strength, rigidity, and toughness of the polypropylene board directly affect its performance. PP boards are known for their high impact resistance, making them suitable for applications that require durability under physical stress. The rigidity of the material is also crucial: if your application demands structural stability, a more rigid board will prevent bending and deformation over time. Additionally, polypropylene boards are lightweight yet strong, offering an excellent balance of strength-to-weight ratio, which is beneficial in industries like automotive, construction, and material handling.
3. Chemical Resistance
Polypropylene boards are highly resistant to chemicals, including a wide range of acids, alkalis, solvents, and oils. This makes them ideal for chemical processing, pharmaceutical, and food industries, where exposure to harsh chemicals is common. When selecting the right board, consider the specific chemicals your application will be exposed to. Polypropylene's corrosion resistance ensures longevity in environments with frequent exposure to chemicals or harsh cleaning agents. For critical applications, it’s important to confirm the material’s compatibility with the chemicals it will come into contact with.
4. Temperature Resistance
Polypropylene boards can withstand a range of temperatures, typically up to 100°C (212°F), though this may vary depending on the grade and formulation of the board. If your application involves exposure to high temperatures, such as in automotive parts, industrial equipment, or exterior applications, it’s important to select a polypropylene board that can maintain its integrity and performance without warping or degrading. For higher temperature needs, additional treatment or a specialized formulation of polypropylene may be necessary.
5. Surface Finish and Texture
The surface finish of the polypropylene board can affect both its aesthetic appeal and functional performance. PP boards typically come in two main finishes: smooth and matte. A smooth surface is ideal for applications where easy cleaning and hygiene are important, such as in food processing or laboratory settings. Meanwhile, a matte finish can be preferable for applications requiring scratch resistance and non-reflective surfaces, such as industrial parts or protective covers. The surface finish also influences printability, so if your application involves custom branding or labels, consider whether you need a board with a surface that facilitates easy printing.
Applications of Solid Polypropylene Board
Solid polypropylene boards, produced through the extrusion process, offer outstanding versatility, making them suitable for a wide range of industrial, commercial, and consumer applications. Thanks to their durability, chemical resistance, and impact strength, these boards are used across various sectors including chemical processing, construction, mechanical parts manufacturing, and custom fabrication. Below are some of the key industries and applications where solid polypropylene boards shine:
1. Chemical Processing & Pharmaceuticals
Polypropylene boards are highly valued in the chemical processing and pharmaceutical industries for their chemical resistance and non-toxic nature. Some typical uses include:
2. Construction Industry
Polypropylene boards are increasingly being used in the construction industry for their chemical resistance, strength, and moisture resistance. Applications in this sector include:
3. Mechanical Parts Manufacturing
Due to their high impact strength, rigidity, and chemical resistance, solid polypropylene boards are widely used in mechanical parts manufacturing:
4. Custom Fabrication & OEM Parts
One of the standout features of solid polypropylene boards is their customizability. They can be easily fabricated into specific shapes and sizes, making them ideal for a wide variety of OEM (Original Equipment Manufacturer) and custom fabrication projects:
5. Food Processing & Packaging
Due to their non-toxic, moisture-resistant, and easy-to-clean properties, solid polypropylene boards are commonly used in the food industry for:
Solid polypropylene boards are a trusted material in various industries, offering a unique combination of strength, lightweight properties, and resistance to chemicals and environmental factors. Their customizability further makes them an ideal solution for a wide range of applications, from manufacturing parts and machine components to creating custom enclosures and protective covers.
Why Choose Polyreflex Polypropylene Board?
Polyreflex stands out as a leader in solid polypropylene board production, offering superior performance, customization, and long-term value.
Choose Polyreflex for reliable, flexible, and cost-effective polypropylene boards designed to meet the unique needs of your project.
Choosing the right solid polypropylene board for your project requires careful consideration of factors such as thickness, mechanical properties, chemical resistance, and surface finish. Polyreflex offers high-quality, customizable polypropylene boards that meet the diverse needs of industries ranging from automotive to construction and custom fabrication. With over 18 years of expertise, we deliver durable, cost-effective solutions tailored to your specifications.
If you're ready to take the next step or need more information, contact Polyreflex today. Our team is here to assist you with quotes, product recommendations, and any questions you may have. Let us help you find the perfect polypropylene board for your project!