Lightweight Yet Strong: Why Car Manufacturers Are Switching to PP Bubble Board
- Share
- From
- https://www.polyreflex.com/
- publisher
- Polyreflex
- Issue Time
- Jun 20,2025
Summary
Discover why leading car manufacturers are switching to PP Bubble Board — a lightweight, durable, and eco-friendly material perfect for trunk floors, door panels, and battery insulation. Learn how Polyreflex's PP Bubble Board enhances performance and reduces vehicle weight.
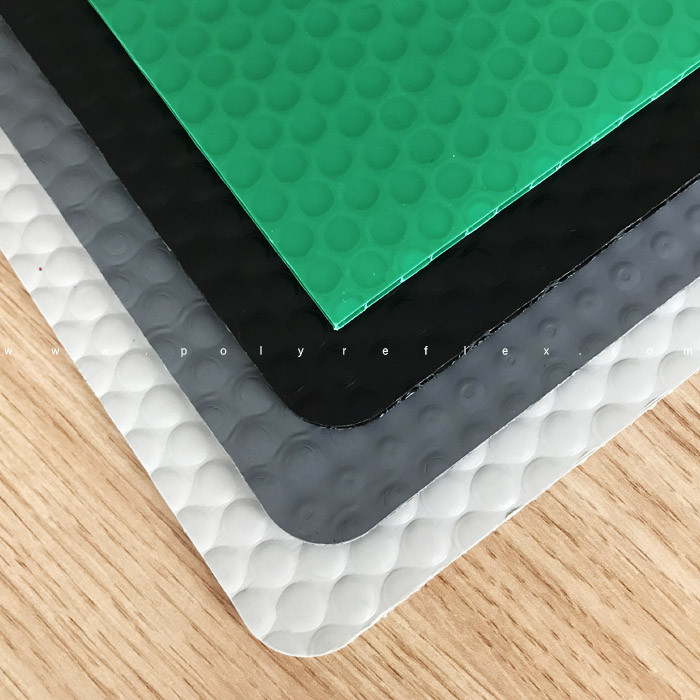
In today's automotive industry, the demand for lightweight and durable materials has never been higher. Car manufacturers are under constant pressure to improve fuel efficiency, reduce emissions, and meet increasingly strict sustainability regulations. One material that is gaining widespread attention for meeting all these needs is PP Bubble Board — a lightweight yet strong polypropylene panel with a unique bubble core structure.
With its excellent strength-to-weight ratio, environmental friendliness, and versatility, PP Bubble Board is fast becoming the preferred material for a range of automotive interior and structural components.
What Is PP Bubble Board?
PP Bubble Board, also known as polypropylene bubble board, is a three-layer co-extruded sheet. It consists of two flat outer layers and a middle layer filled with a bubble-shaped core. This special design provides outstanding rigidity while keeping the overall weight of the board very low.
Unlike solid plastic sheets or hollow boards, PP Bubble Board offers the perfect combination of:
It's a highly engineered material ideal for use in modern automotive manufacturing.
Why Weight Matters in the Automotive Industry
Reducing vehicle weight is one of the most effective ways to enhance performance and efficiency. Every kilogram saved contributes to:
For electric vehicles in particular, lightweight materials are essential to offset the weight of heavy battery systems. As a result, automakers are increasingly replacing heavier components with advanced plastic solutions like PP Bubble Board.
How PP Bubble Board Meets Structural Demands
Despite its low weight, PP Bubble Board offers excellent mechanical strength. The bubble core structure acts as an internal support, distributing pressure and absorbing impact. This makes the board ideal for parts that need to be both strong and lightweight, such as:
Its stiffness and dimensional stability also make it suitable for thermoforming and CNC processing, allowing manufacturers to create precisely shaped automotive parts.
Key Automotive Applications of PP Bubble Board
Here are some common ways car manufacturers are integrating PP Bubble Board into vehicle design:
Trunk Floors and Liners
Lightweight yet strong enough to support cargo loads.
Tool Compartments
Protects tools and accessories while keeping the structure light.
Door Panels and Seat Backs
Helps reduce interior weight without compromising durability.
EV Battery Pack Insulation
Acts as a base plate or barrier layer for battery modules.
Interior Dividers and Covers
Custom-shaped parts used to organize and protect vehicle interiors.
Each of these applications benefits from the board's low density, high stiffness, and resistance to moisture and chemicals.
Advantages Over Traditional Materials
PP Bubble Board is quickly replacing older materials that fall short in performance or sustainability. Here's how it compares:
Traditional Material | Common Issues | Why PP Bubble Board Is Better |
Plywood / MDF | Heavy, absorbs moisture, warps easily | Lightweight, waterproof, more durable |
Corrugated Paperboard | Weak in humid environments, not reusable | Water-resistant, reusable, stronger |
Solid PP or PE Sheets | Heavier, more costly | Similar rigidity at a lower weight and cost |
PVC Foam Board | Heavier, not eco-friendly | Halogen-free, recyclable, lightweight |
By switching to PP Bubble Board, manufacturers can lower part weight, reduce total vehicle mass, and simplify part recycling at the end of a vehicle's life.
Real-World Success: Why OEMs Are Making the Switch
utomotive OEMs and Tier 1 suppliers are already turning to PP Bubble Board for its advantages in cost, sustainability, and performance. In many cases, replacing traditional materials has resulted in:
It's a win-win for both manufacturers and end users — especially in the growing electric vehicle market.
Conclusion
The automotive industry is evolving rapidly, and material choice plays a critical role in vehicle innovation. PP Bubble Board stands out as a next-generation material that combines light weight, mechanical strength, and environmental sustainability.
If you're a vehicle manufacturer or parts supplier seeking a high-performance alternative to wood, PVC, or solid plastic panels, PP Bubble Board is the smart solution.
Get a Free Sample or Quote
Polyreflex is a leading manufacturer of PP Bubble Board in China with 18 years of production experience. We offer customized specifications, fast delivery, and expert support.
Contact us today to request a free sample or quotation!